When Portland, Oregon, opens up a soaring new airport terminal in May 2024, it’s widely expected to become a signature building. Part of the draw will be the sweeping, mass timber construction, including a 9-acre roof boasting gracious curves and skylights.
The project’s uniqueness in no small way is thanks to its supply chain. Every piece of wood was sourced from within 300 miles of the airport, and about half of it came from 13 small and tribal landowners in Washington and Oregon. The process was so exacting, the architects knew every board that frames the skylights above the 26 Y-columns came from the Yakama Nation, and all the double beams in the six massive oval skylights came from the Coquille Indian Tribe.
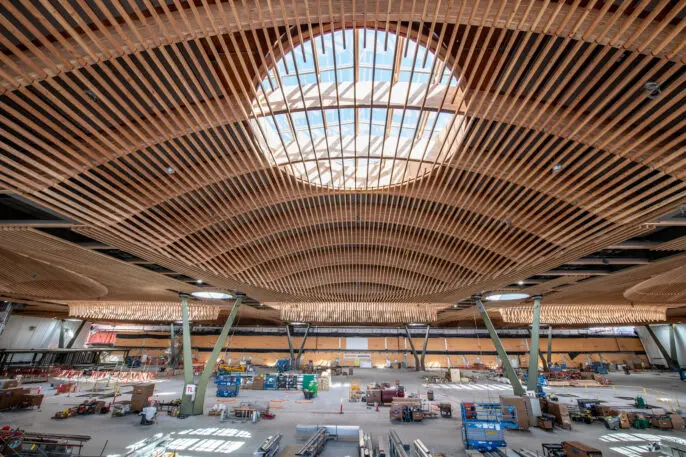
“We’re a natural resource state, and creating that connection into our community was really important,” says Vince Granato, chief projects officer at the Port of Portland.
This forest-to-frame system used for the Portland International Airport sought out more sustainably minded landowners, who supported better forest practices, says Jacob Dunn, principal at ZGF, the firm that designed the terminal.
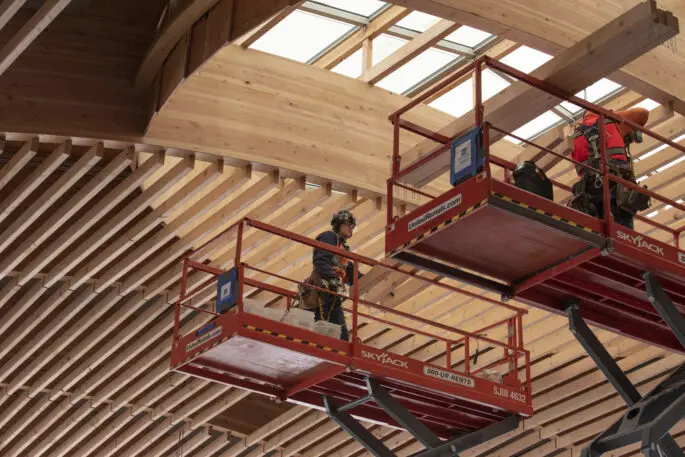
“Architects usually talk to the top of the supply chain, the manufacturers,” he says. “We don’t usually talk to landowners.”
Mass timber buildings—made with compressed wood boasting enough strength to support multistory structures—have taken off in the U.S., as builders, developers, and architects embrace the less carbon-intensive alternative to concrete. Roughly 1,860 such projects have been built already or are in progress. But historically, a vast majority of buildings constructed in this fashion—including the 25-story Ascent MKE in Milwaukee, the tallest such structure in the world—were made with wood imported from outside the U.S.
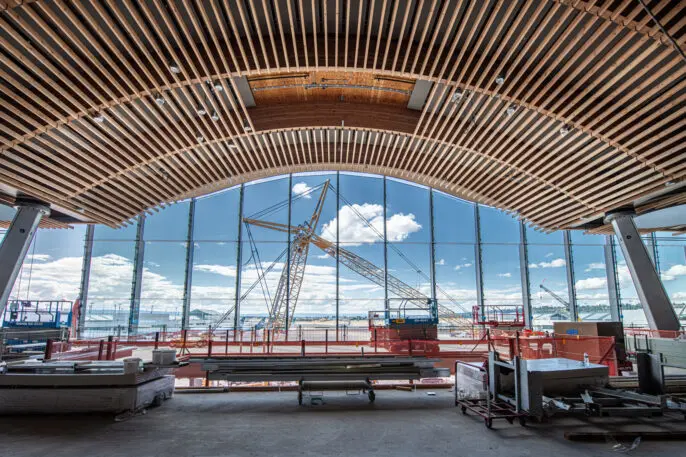
As demand increases domestically and globally—worldwide mass timber sales should triple by 2030 and reach $3 billion annually, per Acumen Research and Consulting—the U.S. could use its own native forests to catch up with soaring demand.
However, the mass timber industry in the U.S. is still in its infancy, says Pat Jolley, product manager for Forisk Consulting’s mill database. U.S. and Canadian production capacity totaled 1.4 billion board feet in 2022, meaning a growing portion of the mass timber needed in North America can be supplied; but it represents just a fraction of the two nations’ total lumber production of 59 billion board feet.
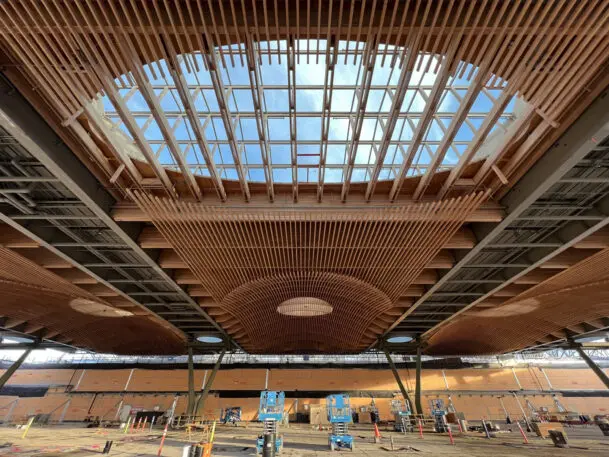
While Europe has been using mass timber since the 1990s, structural issues made the U.S. slow to pick up on it. Deforestation laws in the ’70s shifted the industry to smaller yields and more sustainably raised timber, decreasing the number of mills in operation. In 2016, there were just four plants in the U.S. and Canada making mass timber, according to Bill Parsons, chief operating officer of trade group WoodWorks. Today a dozen U.S. firms can supply mass timber panels, and just about a quarter of such wood is shipped in from overseas.
The cross-laminated timber used in today’s new buildings is created when layers of structural-grade lumber are arranged crosswise and then glued together; they need a higher strength rating and must be dried longer to reduce moisture content. Many existing U.S. lumber mills would be willing to adapt to mass timber demand, Jolley says, but they’re still waiting for the market to achieve critical mass.
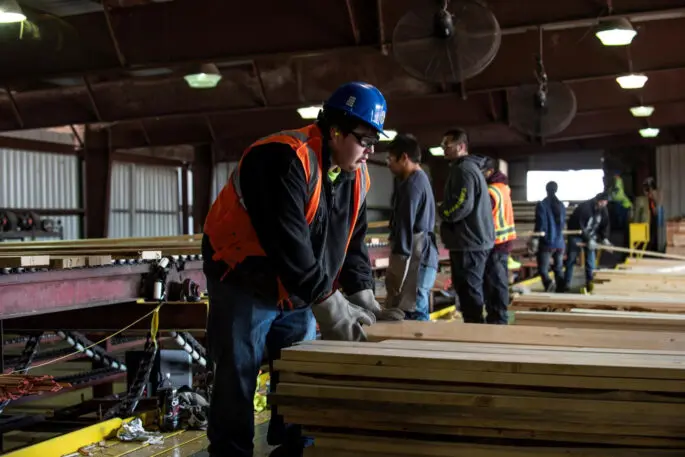
Significant chicken-and-egg type challenges stand in the way. It’s a huge capital expense to open up or convert a facility, and the U.S. lacks enough oversize CNC machines, the computer-controlled lathes used to cut mass timber. At the same time, unlike Europe, which has mostly pine forests, the U.S. has an array of wood timbers growing domestically—Douglas fir, hemlock, southern yellow pine—with different fibers and materiality that make a commoditized, national production line harder to set up.
False starts haven’t helped. Katerra, the unicorn modular construction startup, invested in mass timber before it flamed out in 2021. A potential plan to build a new Walmart headquarters in Bentonville, Arkansas, out of regionally produced mass timber fell through earlier this year. And pre-COVID-19, a spate of large campus projects by the likes of Google and Meta drove up demand for mass timber, which then came crashing down.
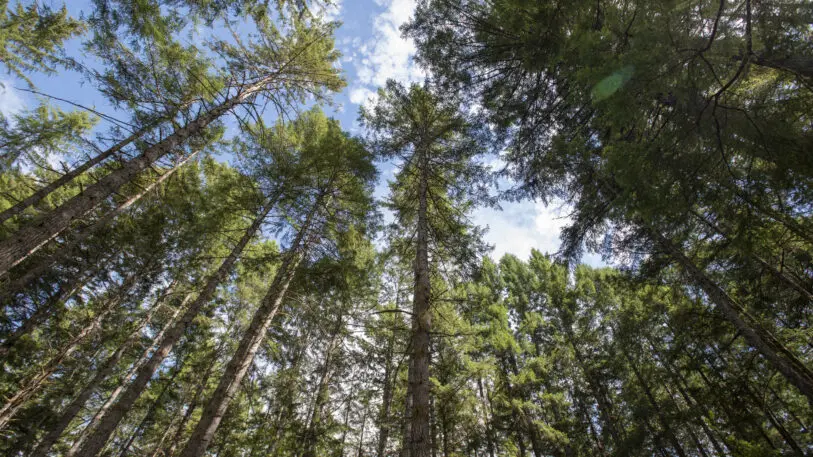
Mass Timber, But Not Mass Manufacturing
Getting the materials for the Portland project wasn’t the only significant challenge. Adding a terminal to a working airport posed its own logistical hurdles. The entire roof was actually assembled on an empty airfield, then slowly moved, million-pound piece by million-pound piece, into place to avoid disrupting operations.
But the timber sourcing proved the most delicate. Timber production is a process that involves landowners, brokers, fabricators, mills, and lumberyards. With the requirement to use specific pieces of timber from small landowners, it meant every stop on the vast chain required segregating the airport trees, which delayed processing. Dunn argues that the extra effort, which wouldn’t have been possible without support from local advocacy group Sustainable Northwest, showed that mass timber doesn’t have to mean mass manufacturing.
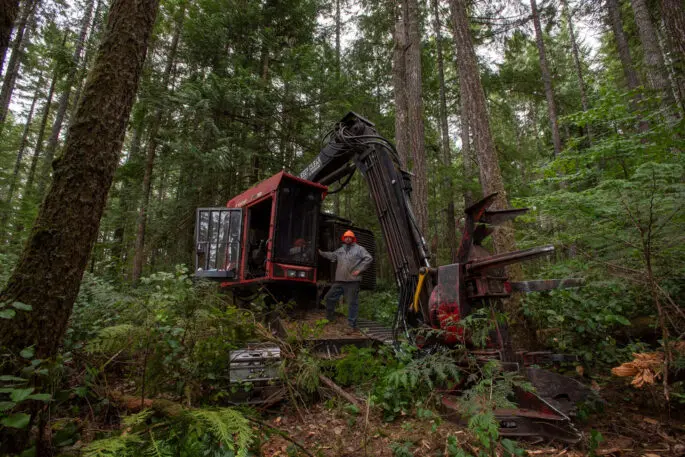
Perhaps surprisingly, Dunn concluded that cutting down on transportation emissions from imported wood was a relatively small advantage. The real benefit came from sourcing from small and tribal landowners who prize environmental stewardship and better land management practices, meaning better land restoration and climate-smart forestry, ecological support, and increased wildfire resilience.
Other developers have had success creating their own domestic supply chains. In Atlanta, the developer Jamestown decided the 619 Ponce office project currently under construction should showcase the region’s southern yellow pine via mass timber construction.
Catherine Pfeiffenberger, Jamestown’s managing director and head of development and construction, was baffled when suppliers told her the process would be more expensive. After she investigated the entire supply chain, she found the 10% premium she was being quoted was just a contingency, reflecting the relative newness of the process; local mills offered a 12-month lead time, while Austrian suppliers said they could do it in half the time, at a 10% discount. Pfeiffenberger went back and pushed all the suppliers to cut out the contingency.
“We had to get in the middle of the supply chain to disrupt it,” she says.
Pfeiffenberger’s efforts meant this improved supply chain had just a 1% increase in costs versus imported wood. Nicknamed “Seedlings to Solutions,” the process starts with wood harvested in Columbus, Georgia, which is sawed into lumber in Albany, Georgia, and turned into cross-laminated timber in Dothan, Alabama, before finally being assembled on-site in downtown Atlanta. Jamestown plans to use this process for future projects in the region.
Continued expansion of local mass timber will require additional worker training, both in the production and the assembly of mass timber building materials. Parsons believes the Portland airport project ultimately shows what’s possible with wood (if setting a slightly unrealistic bar about such specific regional sourcing).
Dunn agrees that it’s hard, but believes that more transparency about where wood comes from—an achievable goal—can help the industry make more sustainable choices. He’s already working with colleagues to create guides and best practices to help others replicate these kinds of sourcing decisions.
And as mass timber becomes more widespread, awareness will drive demand, which will help solve knots in the supply chain. Skanska, an international construction and development firm working on the Portland airport extension, is tracking higher U.S. demand for mass timber schools, police stations, industrial facilities, and residential projects. Seeing this style of construction at an airport has already helped the market take off.
“The Portland project has almost created a market across the country,” says Dean Lewis, Skanska’s director of mass timber and prefabrication. “We’re getting calls from Atlanta and New York asking about the kinds of timber we can get within 300 miles of the city. ‘Can we do that here?’ They all want that local story.”
Recognize your brand’s excellence by applying to this year’s Brands That Matter Awards before the final deadline, June 7.
Sign up for Brands That Matter notifications here.