There were more than a million tons of sawdust with nowhere to go. In Maine, where about 90% of the state is forested, sawmills are one of the state’s main industries. Their sawdust byproduct had typically supplied one of the state’s other main industries, pulp and paper mills.
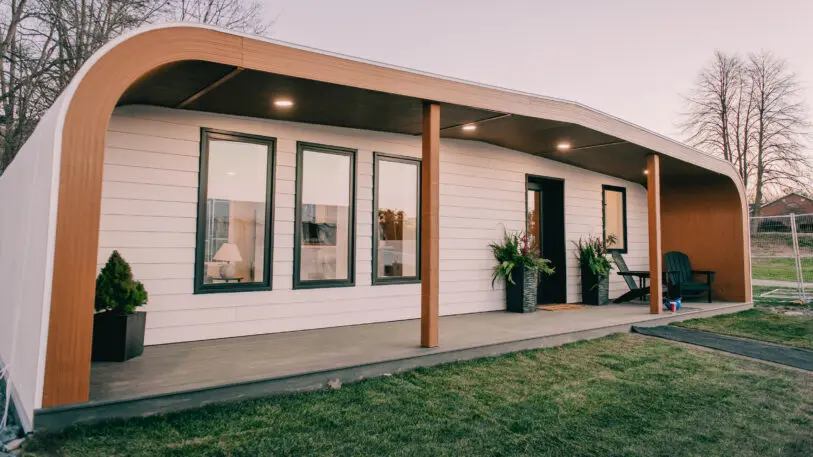
But several of the state’s biggest pulp and paper mills have shut down in recent years, leaving the annual waste stream of more than a million tons of offcuts, wood chips, and sawdust from the sawmills without any takers.
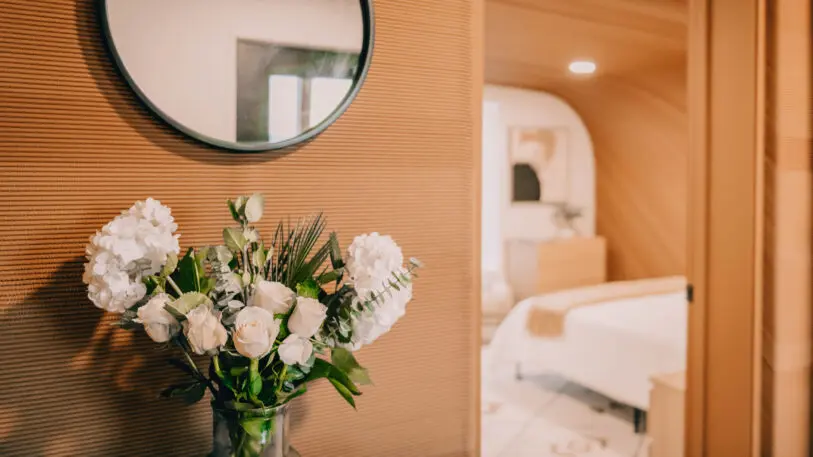
The materials scientists at the University of Maine’s Advanced Structures and Composites Center saw an opportunity. As specialists in combining polymers with emerging biomaterials, they saw the surplus of unneeded wood waste looking like a fresh pile of buildable material.

The Center had recently been tasked with finding solutions to the state’s shortage of affordable housing, which was being exacerbated by pandemic-related supply chain issues and labor shortages. 3D printing seemed like a potential solution. And with the abundant availability of wood waste, university researchers started to wonder if sawdust might be a new kind of building block.
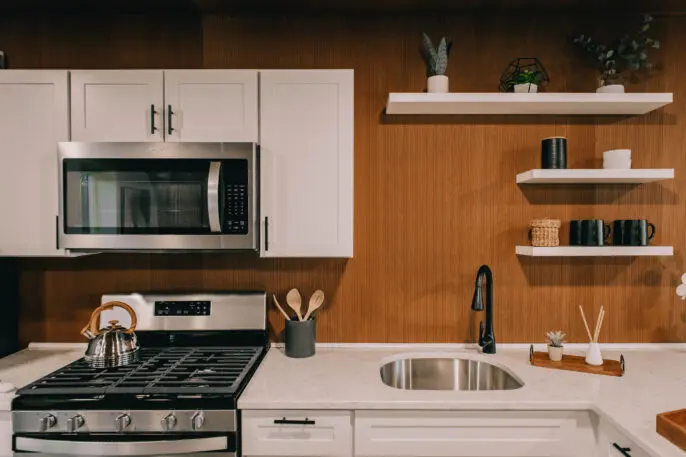
After several years of development, the university’s researchers recently unveiled BioHome3D, a 600-square-foot prototype house that had been 3D printed out of 100% bio-based recyclable material. They combined wood waste and bio-resins to form the base material used by an extra-large 3D printer, which pumped out the entire home, layer by layer, including its floors, walls, and roof. Other wood-based materials were used for its insulation and floor tiles. The house was printed in four modules, which were then transported to a site near the university, in the town of Orono, where they were assembled in about a day.
Habib Dagher, executive director of the Advanced Structures and Composites Center, says the use of wood-fiber feedstock for 3D printing is a sustainable way to build homes, and represents a more comprehensive approach compared to most 3D-printed homes currently entering the market, most of which use forms of carbon-intensive concrete. “They’re not printing the foundations, the roof, the ceilings, the floors—they’re just printing the walls,” he says. “That’s good, but it doesn’t solve the problem of labor.”
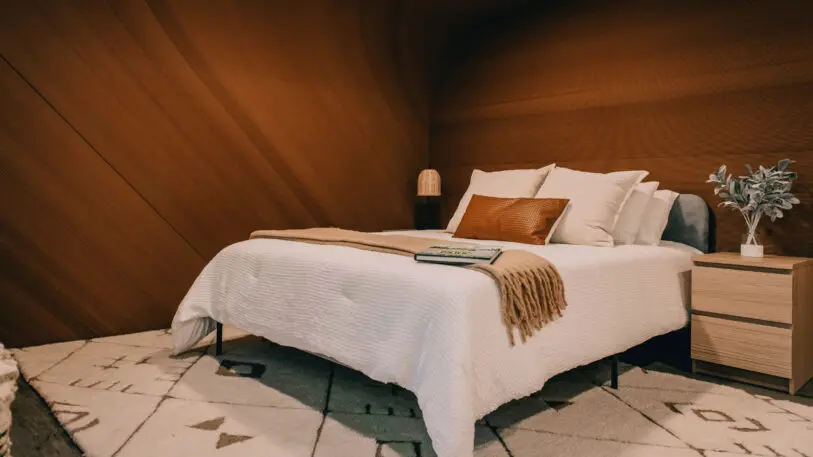
And in cold northern climates like Maine’s, 3D printing homes out of concrete or other geomaterials on site is untenable for large chunks of the year. Dagher says that the wood-and-resin material his center has developed can withstand weather, and its production can be done in factories instead of on building sites.
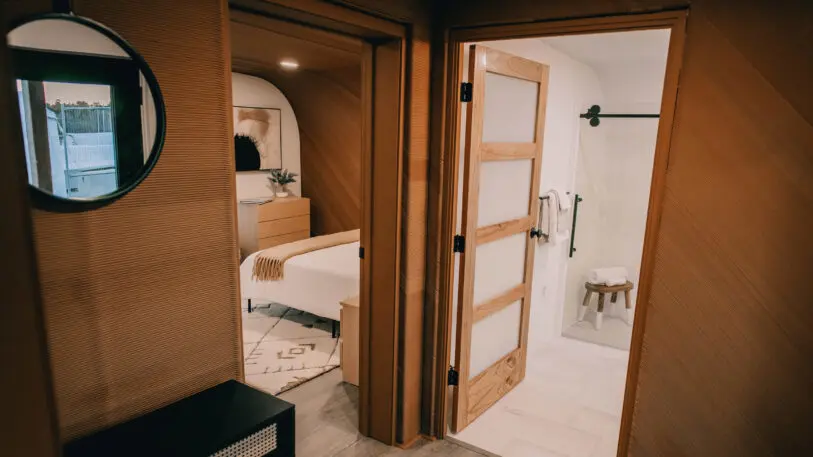
BioHome3D is a full-scale proof of concept. Dagher says the house has been built and furnished like a typical home, and is intended to be a model for this novel production approach, as well as a kind of experiment. “We’ve done all the testing we can think of in our lab. We’ve tortured this material for so many years with freeze-thaw and temperature cycling, and strength. We know it works. But there’s nothing like putting it through a good old Maine winter,” Dagher says.
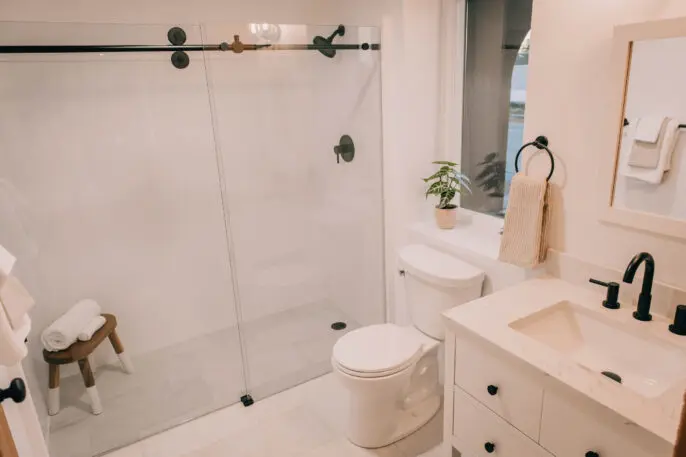
That Maine winter is underway, and Dagher’s team is using it to monitor the house’s performance out in the wild. It’s been outfitted with a variety of sensors that will collect data over the coming months, giving researchers a better sense for how the material reacts to different conditions and informing tweaks they may need to make to the construction process. The data they’ll be collecting this winter will assess structural and thermal performance, as well as airtightness and air quality within the home. They’ve finished some parts of the interior with common building materials, like drywall and house paint, and left others unfinished, to see whether any surface or aesthetic issues arise. And with winter temperatures in this part of Maine often dipping below zero degrees Fahrenheit, the house will have plenty of cold and snow to contend with.
Other test houses will follow. Dagher says the Advanced Structures and Composites Center has already raised $80 million to develop a new research factory where it can figure out how to scale production, pushing the 3D-printing machinery to pump out up to 500 pounds of material per hour. Dagher says the factory should be up and running by the end of 2023.
“Our goal is to produce one house every 48 hours,” he says.
Recognize your brand’s excellence by applying to this year’s Brands That Matter Awards before the early-rate deadline, May 3.