Perched over a ravine in the mountains of Los Angeles is an innovative new pedestrian bridge designed by architecture students and built with the help of new robotic technology. The bridge is an example of how the construction of bridges and buildings can be rapidly accelerated and pushed to new limits of design.
Originally the subject of a design studio at the University of Southern California School of Architecture seven years ago, the project evolved from a speculative exercise into an actual piece of urban infrastructure. Construction on the project was completed just before the pandemic, and images are now being released publicly for the first time.
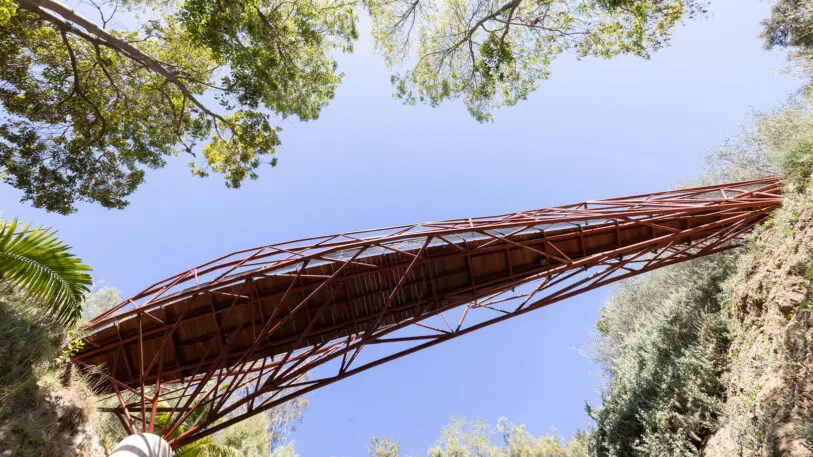
The Arroyo Bridge looks like a bird’s nest assemblage of rust-colored steel tubes; it reaches 80 feet across an oak-lined canyon. Designed by students with 3D software, fabricated out of hundreds of steel parts by an advanced six-axis robotic arm, and then assembled into large pieces that were welded together on-site, the bridge is a prototype for a new method of fabricating architecture that reduces waste and streamlines construction.
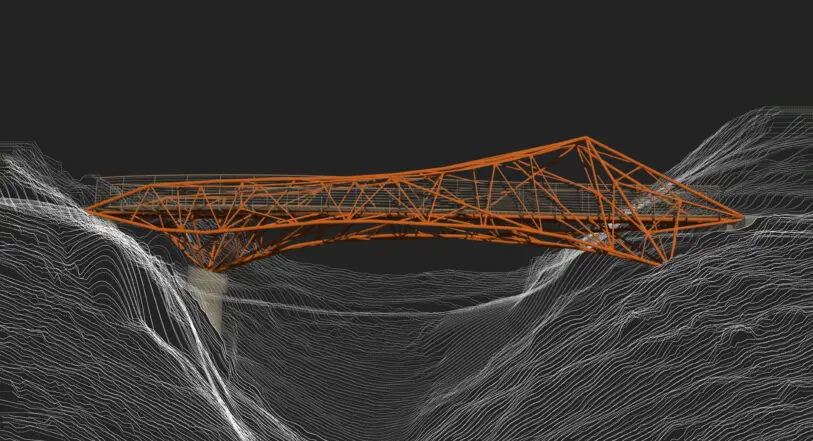
“This is the future. It gives more creative freedom to designers to work directly with fabricators,” says R. Scott Mitchell, an associate professor at the USC School of Architecture who led the studio that designed the project, in partnership with the 3D design and engineering software company Autodesk.
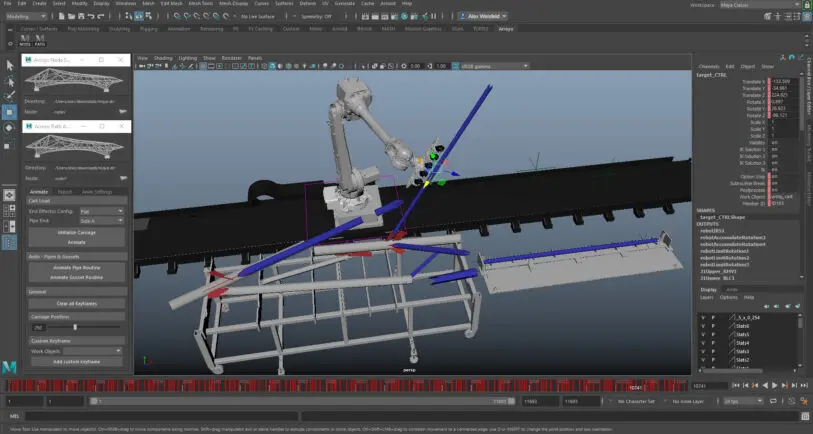
The project started in spring 2014 when Mitchell was approached by architect and fellow USC instructor David C. Martin. Mitchell had taken over the furniture fabrication course that Martin had begun teaching in 2005, and Martin had a suggestion for a different kind of challenge. Instead of fabricating furniture, Martin suggested having the students design a bridge for a remote site in the mountains of Los Angeles. As the former design principal of L.A.-based AC Martin Partners, an architecture firm started by his grandfather in 1906, Martin has had a lifelong interest in architectural innovation. For Mitchell, founder of the architectural fabrication company Gigante AG, the project sounded like an ideal way to explore new approaches to building at a large scale.
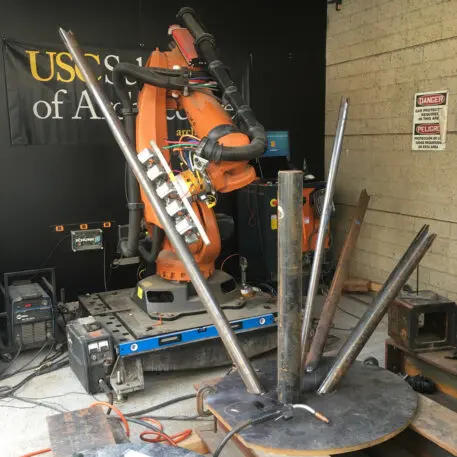
By the end of that semester, the students’ collaborative design of the bridge was more than just a clever model, but rather the makings of a project that could be built at scale as a prototype. Martin was intrigued. Through Madworkshop, a nonprofit design education foundation Martin cofounded with his wife, Mary, they sponsored further development of the idea. Mitchell soon had six students working over the summer to figure out how the design could be fabricated and built. They eventually found that with the right technology they could create a design for the bridge that would reduce its component parts to about 500, and that those parts could be specially fabricated to combine into segments that could be easily transported to the remote site.
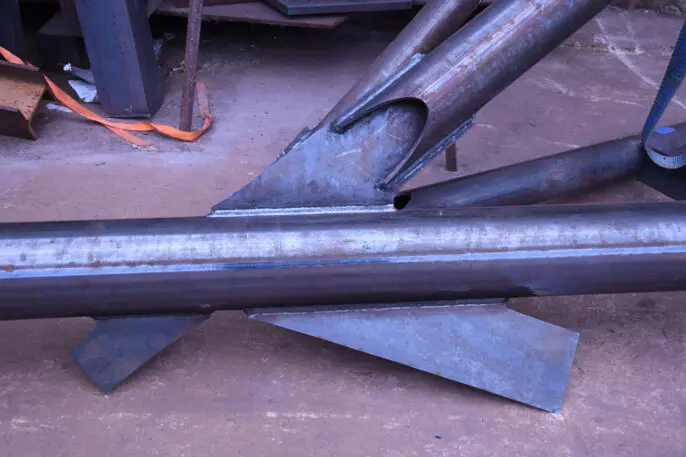
“Scott came to me one day and said, ‘I think we’ve got to use robots. That’s the only practical way to do this.’ And I thought to myself, Oh god, where is this going to take us?” Martin says.
It led the project and its designers on a long journey. Because USC’s facilities weren’t large enough to accommodate the full-scale build-out of the bridge, or the complexity of the fabrication, several architecture students ended up moving to Boston for about seven months to work directly with Autodesk at its architecture, engineering, and construction technology facility. Mitchell flew back and forth from L.A. every week, cramming 40-hour weeks into a handful of days and refining the robotic scripting to optimize the fabrication and construction efficiency. Using Autodesk’s technology, Mitchell and the students managed to coax the robotic fabricators to create welds and fittings that ended up having a precision of within 1 millimeter of the digital design—crucial for a structure as detailed as a bridge. “We were really developing new welding processes for this bridge. We literally had to invent something every day,” Mitchell says.
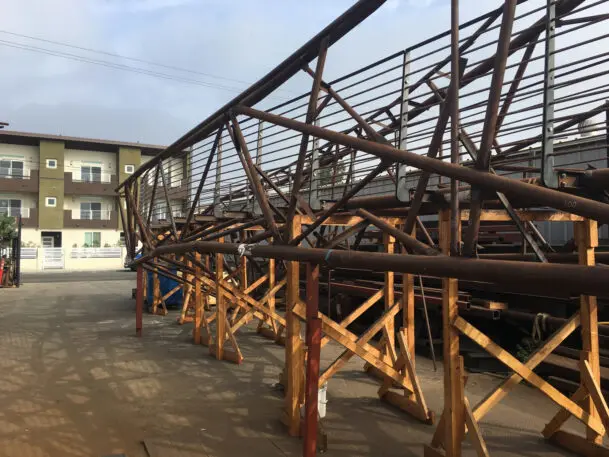
Once the robotic fabrication was set, the 500 steel components of the bridge were welded by the robots into about 30 chunks that were then loaded on trucks and sent across the country to L.A. After a test assembly at a nearby warehouse, the pieces were brought out to the mountainous site for construction. Because of its natural setting, the site was not readily accessible. The pieces were trucked to the end of the road near the canyon and then hauled up to the site on a telehandler, which looks like an all-terrain vehicle combined with a forklift. The parts were carefully placed on piles that had been dug into the terrain, and within about seven days the entire 80-foot-long bridge was snapped into place. After another two weeks of welding, it was completed in May 2020.
Mitchell says the robotic fabrication and welding helped the project eliminate most of the construction waste that would typically result from similar construction, with no temporary formwork required to position parts for mounting and welding. The bridge is made up 18,000 pounds of steel, and created only 1,000 pounds of waste material, all of which was recycled, according to Mitchell. For other construction projects, which produce a notoriously large amount of waste, this process offers a more environmentally friendly pathway.

Since the project’s start in 2014, students have come and gone but several were involved throughout, working on the initial design and then participating in its construction. Mitchell says this kind of practical experience is rare in architectural education. But it’s also time-consuming. Just getting the project through the permitting process with the city of Los Angeles took three years. He wouldn’t disclose the total budget for the project, but notes that as a prototype it had a higher cost than a more traditionally built bridge. The project was more about experimenting and proving that the process could work than keeping the budget down. That part can come later, he says.
The bridge is the rare student-designed prototype that’s actually been built, and it hints at the power that this type of collaborative robotic fabrication can have. Once refined, the process may see robots milling and welding the pieces of even bigger structures. Martin says that using robots to assist in the fabrication and construction of complex or even simple buildings and infrastructures is only beginning to show its potential.
“The whole process could be automated. Instead of a huge expense and huge construction waste, it could become something that was highly thought out ahead of time and measured, and the physical process of making it would be highly efficient,” Martin says. “That’s been the promise of industrialization, with computers and robots, and this bridge proves that absolutely you can do this.”
Recognize your brand’s excellence by applying to this year’s Brands That Matter Awards before the early-rate deadline, May 3.