The Canadian Scouts motto is “Do your best,” but in the midst of the coronavirus crisis, even that can be a tall order.
Not for Quinn Callander. The 12-year-old Scout lives in the suburbs of Vancouver, Canada, and heard a local hospital ask for help with a unique problem: Its healthcare workers had serious ear pain after long shifts wearing masks nonstop. So he put his 3D printer to use.
Masks are crucial for curbing the spread of COVID-19, particularly among medical personnel. But as we’ve reported, most commercially available masks aren’t particularly well-designed. Case in point: When you wear a mask all day, it puts pressure on the head and causes friction against the ears.
Callander developed a simple but effective “ear guard” that prevents the elastic bands on a mask from rubbing against the backs of people’s ears. He prototyped several designs with his 3D printer, based on a design he found on the open-source 3D printing community Thingiverse. He landed on a wide plastic strap that goes around the back of the head. The strap has notches so the wearer can loop the mask’s elastic straps around whichever notches are most comfortable, allowing them to adjust the tension while keeping the mask firmly in place.
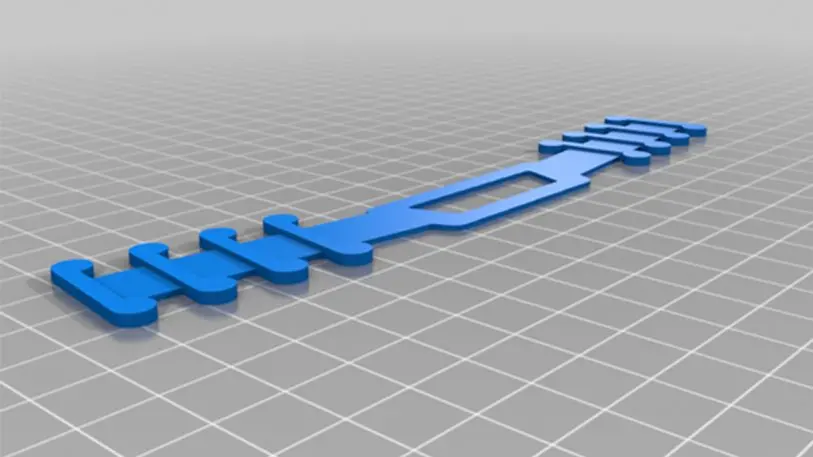
Callander points out that this strap is a good way for people with 3D printers to contribute to the cause without competing for the transparent plastic required to make face shields, which are in high demand. His bands are made from polylactic acid, the most commonly used plastic material for 3D printing, and are relatively cheap to make. “So seek out your local health care providers, ask if this would help them, and get your printers going!” Callander wrote on his Thingiverse post.
Recognize your brand’s excellence by applying to this year’s Brands That Matter Awards before the early-rate deadline, May 3.