Think about classic blue jeans. The rich color comes from indigo, and it’s so ubiquitous both in fashion and in the American cultural imagination that it’s easy to imagine denim cloth as a naturally occurring phenomenon.
It’s not. To get that blue-jeans hue, the yarn that’s eventually woven into denim has to be pulled through a dozen boxes, each filled with up to 2,000 liters of liquid dye and water, lined up to reach the collective length of a football field. Textile threads require multiple exposures to indigo dye to truly absorb the color, and this system is used across the industry as the foundation for one of the most popular pieces of clothing across the world.
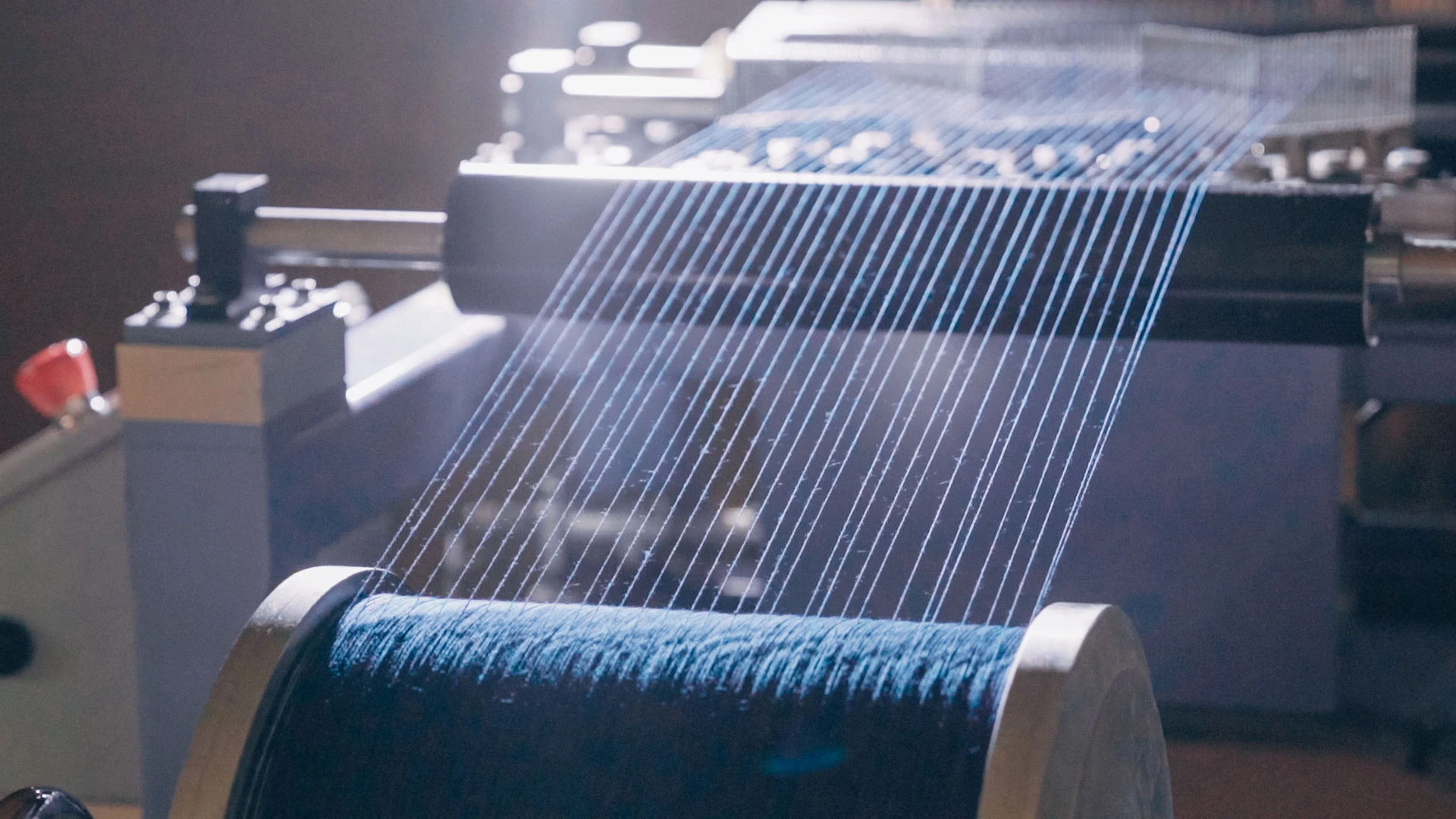
Wrangler, which has been making western-style blue jeans since 1947, is now breaking with this manufacturing tradition. The brand, along with jeans company Lee, was an early investor in a new method of denim dyeing, developed at Texas Tech, that foregoes the yards of dye vats for a more streamlined process that transmits indigo dye via foam.
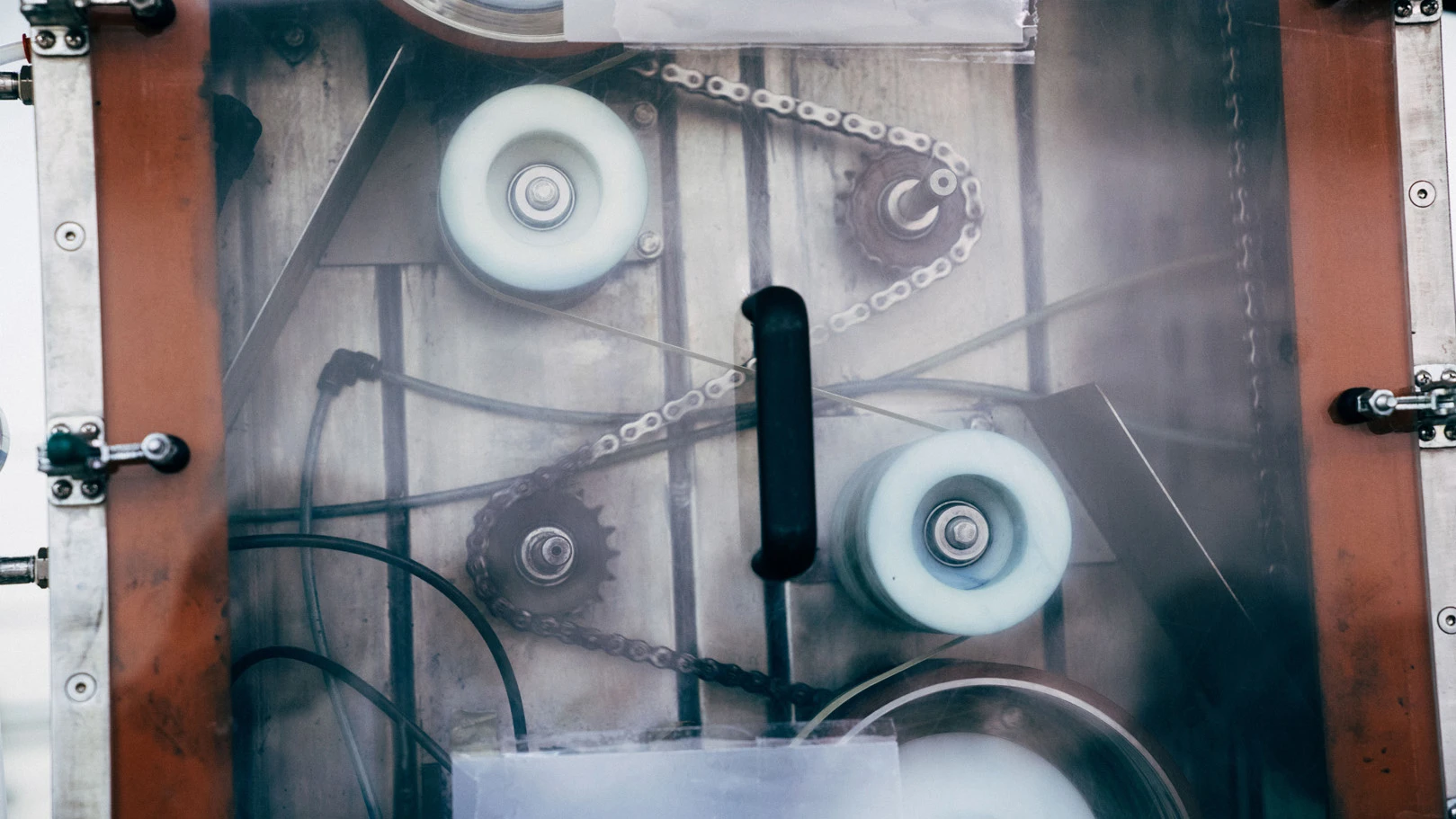
“The significance of this new foam-dye process is really predicated on what it replaced,” says Roian Atwood, Wrangler’s director of sustainability. The company estimates that the new method, which they call “Indigood,” eliminates over 99% of water from the dyeing process. In the foam-dyeing method, the yarn is passed through three chambers, where its sprayed with foam infused with indigo dye. The chambers are completely sealed and filled with nitrogen, which helps the dye absorb into the yarn. To roll out this innovative new dyeing process, Wrangler worked with a mill in Valencia, Spain called Tejidos Royo, that became the first textile operation to host the new method.
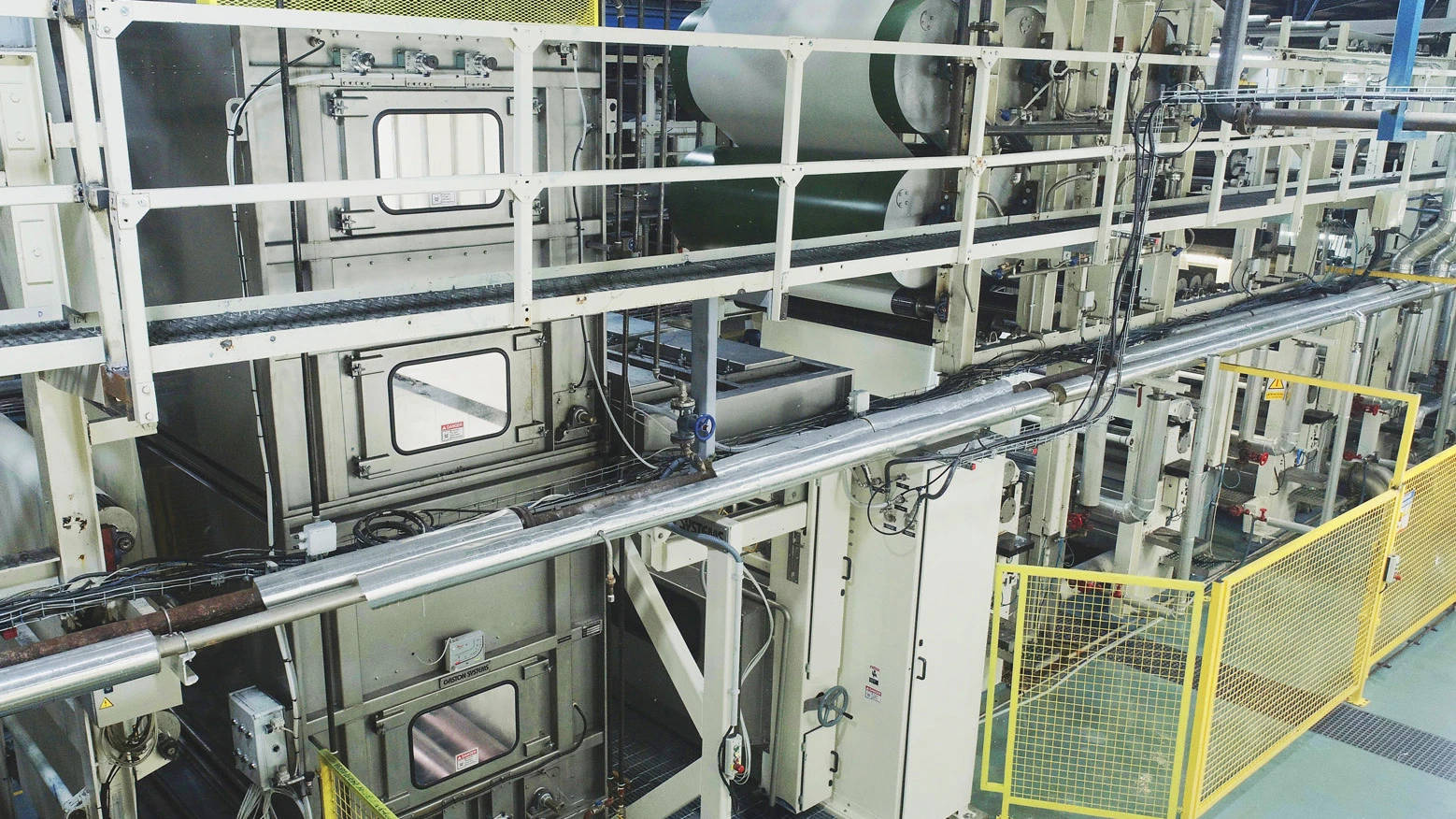
Not only does the foam dyeing method do away with the potential for water waste at the end of the manufacturing process, which is one of the most environmentally damaging aspects of one of the world’s most resource-intensive industries, but it drives down energy usage, too. According to Wrangler, the foam dyeing process requires 60% less energy and mitigates waste by the same percentage.
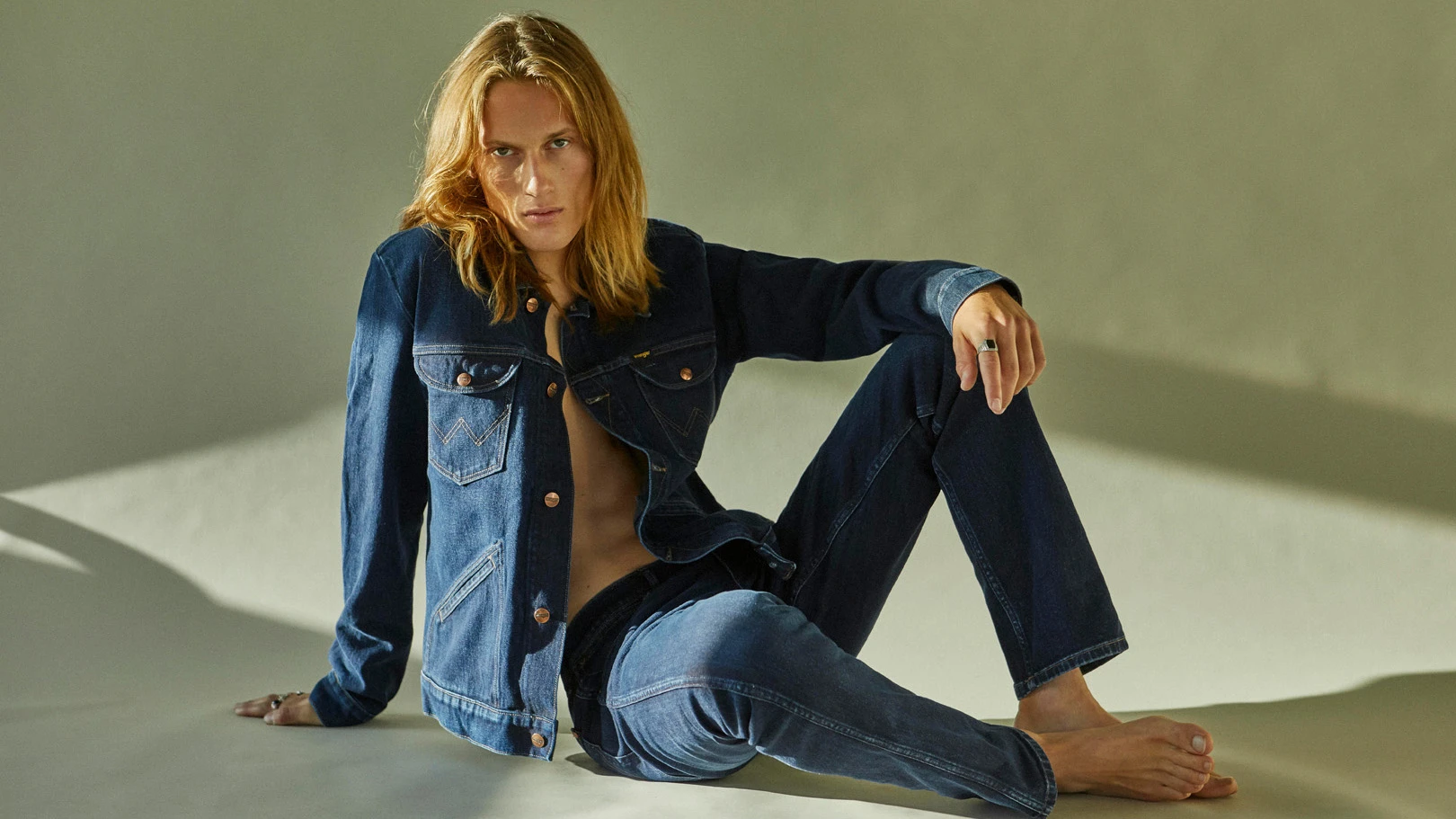
For now, the Indigood denim will only be available through Wrangler’s premium line, Icons. Availability is limited because of the production capacity of their manufacturing partner, but eventually, Atwood says, the aim is to scale the new dyeing method across more Wrangler products, and hopefully, the industry.
Recognize your brand’s excellence by applying to this year’s Brands That Matter Awards before the early-rate deadline, May 3.